Traditionally, rubber and urethane covers on rollers were used to handle the strip, sheet, and plate material through the process line or machine. APT offers non-woven rolls that deliver savings and performance advantages over conventional rolls.
Innovation is the driving force behind APT’S Non-Woven Mill Rolls. We hired a think tank of Non-Woven Mill Roll experts to design around the short comings of the past and current technology on the market. We developed a binder that coats the Non-Woven material and handles the environments and applications of todays mills and auto stamping plants. We continue to optimize solutions and technology with teams working out in the field with customers and teams in the lab to continually develop new solutions.
Apt non-woven mill roll advantages
Why our mill rolls are superior to the conventional rubber rolls
Longer life and repairable, resistant to cuts and gouges leading to increased up-time
Open ‘more porous’ surface design allows for consistent strip contact and higher line speed
Self-healing for superior fluid control to the traditional rubber rolls which allow cuts to propagate
Higher coefficient of friction on many surfaces (incliding wet & oiled) for better strip control
Details
Benefits
Benefits
Economic Benefits:
- . Higher line productivity
- . Visible quality improvements
- . Higher strip speeds
- . Considerably longer roll life
- . Less downtime of line
- . Much lower maintenance expenditure
- . Low set-up costs
- . Less Scrap
- . Substantial overall cost savings
Technical Benefits:
- . Extremely Shear resistant and elastic surface
- . Roll surface cannot be destroyed by distortion
- . High nip pressure reserves, therefore no danger of burning or destroy ing the roll covering by strip buckles or twisting
- . Roll surface does not become glazed, like rubber, polyurethane, or similar coated rolls
- . Constant, extremely high friction values to achieve high tension and precise steering control
- . No hydroplaning
Environmental Benefits:
- . Carry-over in wringing/squeezing applications will be greatly reduced
- . Time between replacement of the cleaning and rinsing solutions, such as demineralized water, acids, and alkalis are substantially longer
- . Up to 50% lower oil consumption due to more uniform oiling or more effective de-oiling
- . Much lower costs for disposal of liquids
- . Cleaner line
Technical Info
Technical Information
What are Non-Woven Mill Rolls?
- . Millions of nylon fibres are extruded into a chamber and blown into the air so they lay randomly
- . This then forms a carpet of material that is coated with certain binders to protect the fibers from different environments
- . Discs are cut out, compacted, and assembled on a shaft using flexible resins
- . These resins are made to be resistant to erosion, flexible and porous, resistant to impacts and cuts
- . Because of the way the rolls are manufactured and designed, they are what the industry calls, ” Self Healing”
- . This means that when the sharp edges and occasional small burrs come through the roll, causing small cuts, the roll is able to repair itself
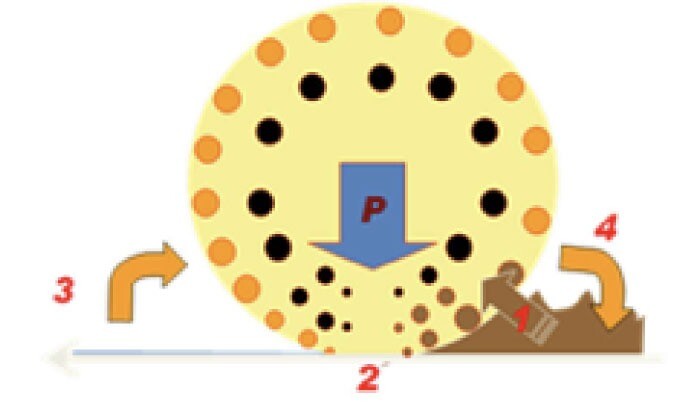
In the Graphic Above:
- . The yellow circle is the APT NON-WOVEN Mill Roll
- . The “P” (inside the blue arrow pointing down is for pressure)is the shaft applying pressure evenly on either side, down on the strip or plate
- . The strip is running from right to left.
The mill roll’s job is to keep the brown fluid on the right side of the roll and leave the left side dry.
How it Works!
#1 – The porous cover absorbs part of the fluid reducing the hydraulic pressure
#2 – Porous surface absorbs the fluid, like a sponge when the pressure decreases
#3&4 – When the cover is compressed again, it gives off the absorbed fluid
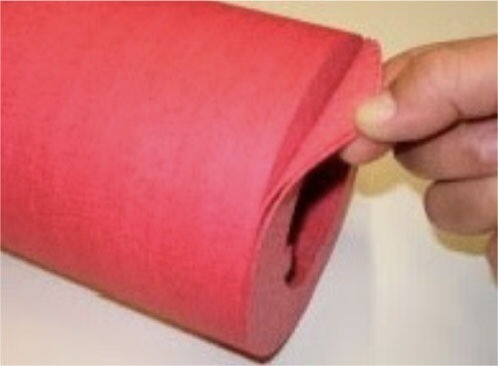
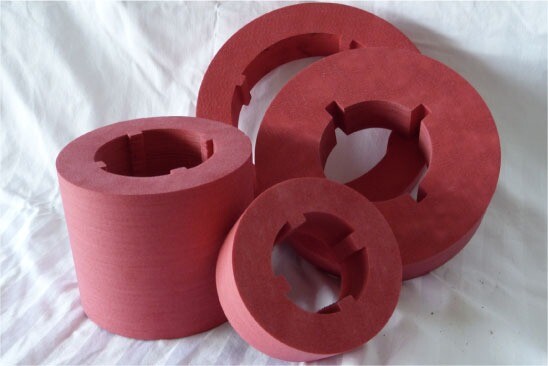
Non-Woven Rolls are “Self Healing”
This means they are porous and able to absorb debris on the strip, which reduces the risk of marking on the metal strip.
- . Rolls are resistant to cuts and gouges
- . The roll compressible and better able to conform to variations in gauge thickness
- . Tight contact across the metal strip produces uniform wringing which significantly reduces chemical carry-out from tank to tank and reduces the need for drying
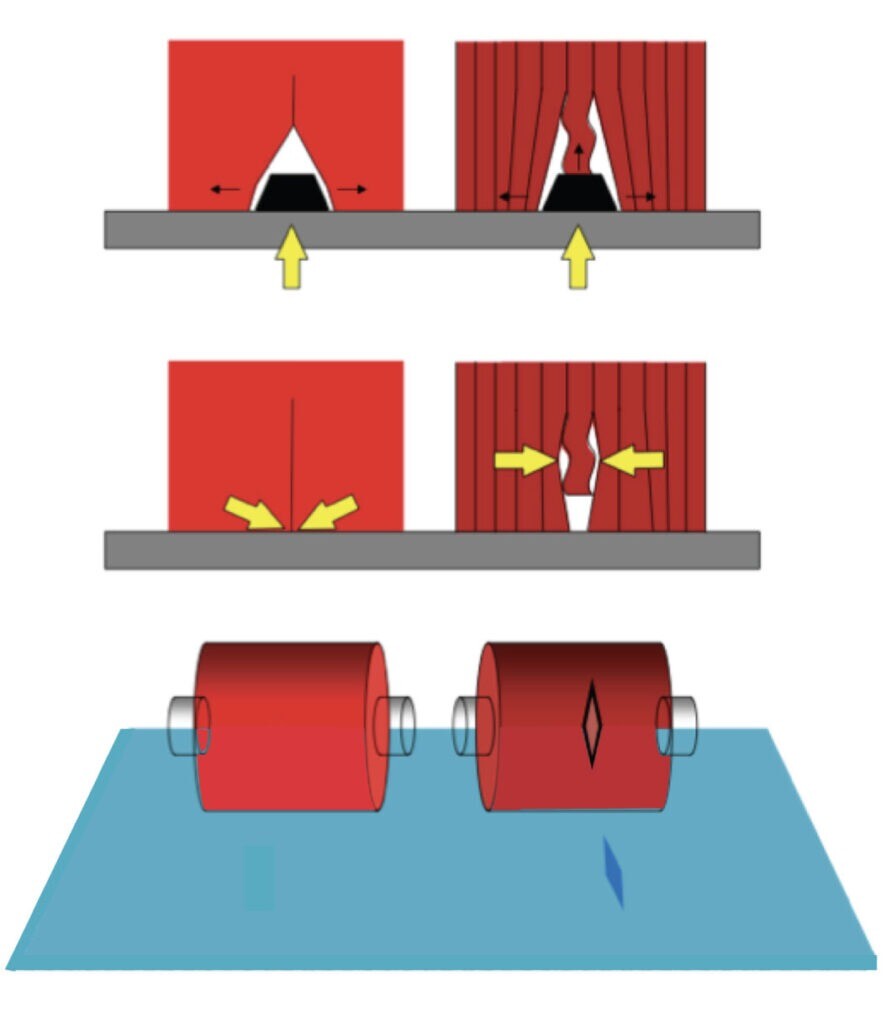
The rolls have up to 24 times greater coefficient of friction compared to rubber
or urethane rolls to improve:
- . Material control by reducing metal coil slippage and hydroplaning
- . Chemical disposal costs and the need to add chemicals are reduced
- . Reduces slipping for better line control
- . Tighter coils
- . Minimized sag
- . Improved line control
- . Straighter edge registry and reduce droop
- . Less slipping overall which = fewer defects on the strip surface
COEFFICIENT OF FRICTION:
NON-WOVEN ROLLS VS. RUBBER ROLLS
APPLICATION | APT PREMIUM RED NON-WOVEN MILL ROLLS | RUBBER |
---|---|---|
DRY | 1.00 | O.69 |
OILED STEEL | 0.69 | 0.02 |
DRY | 1.00 | 0.69 |
OILED ALUMINIUM | 0.58 | 0.02 |
Applications
Applications
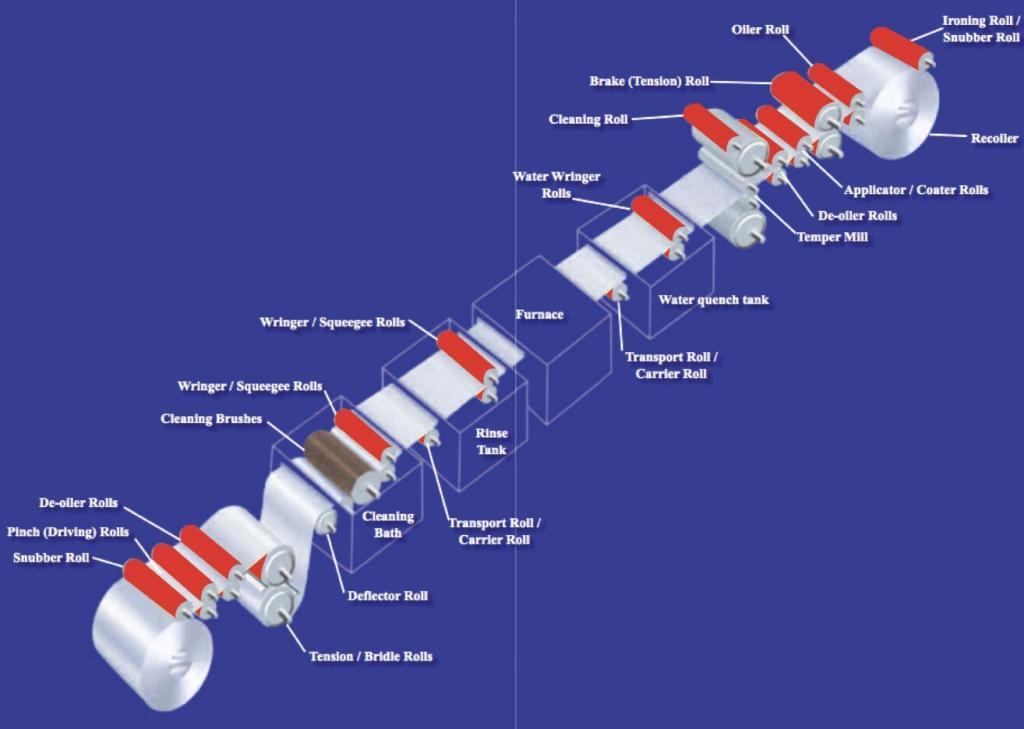
Where do you find Mill Rolls in your process line?
. Oiler Rolls
. Applicator Rolls
. Wringer Rolls in rinse tank
(Cleaning Section)
. Wringer Rolls in rinse tank
(After Plating)
. Oiler Rolls
. Wringer Rolls following quench
. Wringer Rolls in rinse tank
. Wringer Rolls in final cleaning section
. Rolls used for rolling fluid retention
. Oiler rolls on recoilers
. Squeegee rolls to clean work rolls
. Oiler Rolls on recoilers
. Rollers used for rolling fluid retention
. Wringer rolls in exit rinse (after painting)
. Wringer rolls in rinse tank (after caustic cleaning prior to paint)
. Applicator rolls
. Wringer/Squeegee rolls in rinse stations of pre-treatment and cleaning sections
. Wringer/Squeegee rolls in final rinse stations after coating/painting/lacquering
. Deflector rolls
. Tension/Bridle rolls
. Wringer/Squeegee rolls in rinse stations after degreasing/ cleaning sections
. Wringer/Squeegee rolls in brushing machines
. Wringer/Squeegee rolls in rinse stations after pickling/ after galvanizing
. After phospating
. Oiler rolls
. Deflector rolls
. Tension / Bridle rolls
. Wringer / Squeegee rolls in final rinse stations before strip drier
. Wringer / Squeegee rolls in rinse stations
. Oiler rolls
. Pinch (Driving) rolls
. Tension / Bridle rolls
. Brake (Tension) rolls
. Oiler rolls
. Feed rolls
. Pinch (Driving) rolls
Embossing Lines
. Feed Rolls
. Pinch (Driving) rolls
. De-oiler rolls
. Oiler rolls
. Wringer/Squeegee rolls in rinse stations
. De-oiler rolls before cleaning section
. Tension Rolls
. Oiler Rolls
. Wringer rolls after water quench
. Wringer rolls in rinse tank (cleaning section)
. Wringer rolls after water quench
. Wringer rolls in rinse tank (cleaning section)
. Wringer rolls in rinse tank (after caustic cleaning)
. Wringer Rolls in cleaning section (after tin plate)
. Pass line rolls at recoiler
. Wringer rolls (rinse section)
. Stainless steel lines
. Oiler rolls
. Wringer rolls for non-ferrous acid and rinse
. Wringer/Squeegee rolls in rinse stations of pre-treatment and cleaning sections
. Wringer/Squeegee rolls after water quench
. Wringer/Squeegee rolls after wet temper mill
. Wringer/Squeegee rolls in rinse stations of
after- treatment section
. Oiler rolls
. Deflector rolls
. Tension/Bridle rolls
. De-oiler rolls (entry and exit side)
. Emulsion wringer / squeegee rolls (entry and exit side)
. Oiler rolls before recoiler
. Pinch (Driving) rolls
. Cleaning / wiping rolls on back-up rolls
. Speed-o-meter rolls / measuring wheels
. Wringer / Squeegee rolls in rinse stations after degreasing / cleaning sections
. Wringer / Squeegee rolls in brushing machine
. Wringer / Squeegee rolls after water quench
. Wringer / Squeegee rolls in final rinse stations
. Oiler rolls
. Deflector rolls
. Tension / Bridle rolls
. Wringer / Squeegee rolls in rinse stations of pre-treatment and cleaning sections
. Wringer / Squeegee rolls in final rinse stations after tin plating
. Oiler rolls
. Deflector rolls
. Tension / Bridle rolls
. Wringer / Squeegee Rolls
. De-oiler Rolls
. Oiler Rolls
. Entry Feed Rolls
ADVANTAGES OVER TRADITIONAL RUBBER COVERED ROLLS
WRINGER / SQUEEGEE ROLL
- . Excellent wringing / squeezing performance
- . Up to 95% reduction in carryover of solutions compared to rubber or polyurethane coated rolls
- . Up to 100 times longer life in comparison with rubber or polyurethane coated rolls
- . Normally a drive motor is not required
- . No hydroplaning
- . Non-marking roll surface
- . No scratching of the work piece surfaces
- . Roll surface is resilient and extremely resistant against cuts from work pieces
- . “Self-healing effect” of the roll covering in case of cuts caused by strip edges, tack welds, or welding seams
- . Very long life
BREAK, BRIDLE, STEERING, TRANSPORT, PINCH, DEFLECTOR, TENSION ROLLS
- . APT Polyspun Non-woven Rolls build up controlled tension levels due to their high frictional values
- . Rubber, polyurethane, and steel rolls do not have enough friction to pro duce sufficient tension
- . Leads to marks or scratches caused by speed differences between roll and strip, Common when strip is wet or oiled
- . This is caused because the roll surface is not porous and a liquid film forms causing aquaplaning
- . APT Polyspun Non-woven fibre covering have up to a 40% void volume
- . The solution is absorbed creating better contact and thus a higher frictional value
- . “Self-healing effect” of the roll covering in case of cuts caused by strip edges, tack welds, or welding seams
- . Very long life
STAINLESS STEEL Z-MILLS
- . In intermediate passes, there are line speed limitations because too much oil left on the strip, produces bad edges when recoiling, this also lead to high oil consumption
- . On the final pass, when up-coiling, too many fines and oil on the strip surface, will create issues in the degreasing section on the next coil processing line
OILER ROLLS
- . Applying a definable streak-free oil film
- . Easy control of the oil film by adjusting the contact pressure of the rolls
- . Up to 50% lower oil consumption
- . Non-marking roll surface
- . No scratching of the work piece surfaces
- . Roll surface is resilient and extremely resistant against cuts from work pieces
- . Very long life
- . Cleaner line / plant
- . Safer line / plant
DE-OILER ROLLS
- . Very effective and uniform squeezing of oil or emulsion
- . Control of the residual oil film by adjusting the contact pressure of the rolls
- . No aquaplaning / hydroplaning effect
- . Non-marking roll surface
- . No scratching of the work piece surfaces
- . Roll surface is resilient and extremely resistant against cuts from work pieces
- . Long life
- . Cleaner line / plant
- . Safer line / plant
Service
Service
As part of our service, APT uses hardware and software to determine TIR and synergistic measurements to determine a final products quality.
Analysis of the results leads to optimization of the roll, shaft, and process.
- . Complete rolls including bearing units
- . Manufacturing of shafts for rolls
- . Checking and refinishing of worn-out rolls
- . Re-coating of worn-out rolls
- . Examination, repair and replacement of shaft journals, fittings and accessories
- . Advice for application and development of customer specific solutions
- . Full service with transport, documentation, etc
Custom Roll Shipping Boxes
We will design, engineer, and manufacture custom steel boxes to meet your requirements. These boxes offer a robust construction and can be designed to secure the rolls by either the journals or bearing blocks in place. These boxes offer the security that the rolls are received by our customers in perfect condition that they left from our facility.