Blog
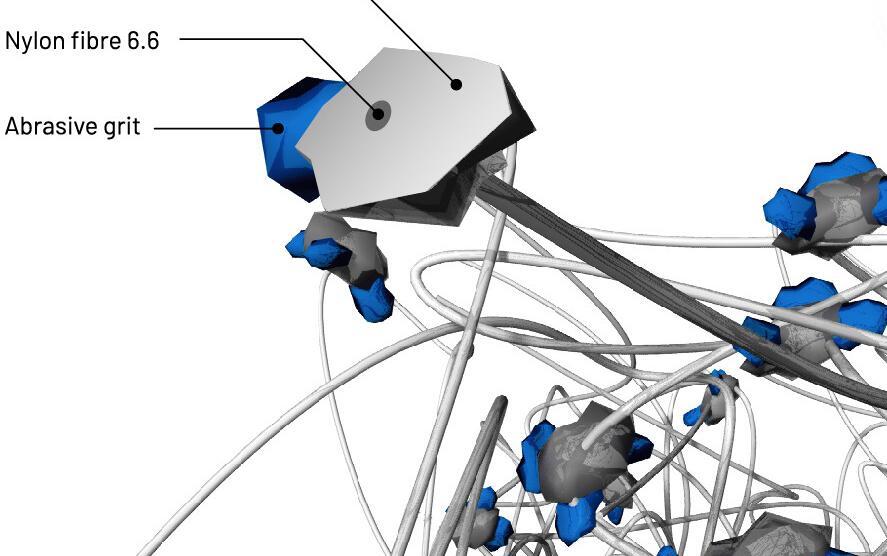
MANUFACTURING NON-WOVEN ABRASIVE BRUSHES FOR SURFACE CONDITIONING
Non-woven abrasive brushes are manufactured by taking a patented nylon synthetic fiber and extruding various diameter thicknesses, cutting them into short lengths, and putting them in a tank that blows the fibers up in the air and then allows them to settle in a random pattern.
The three dimensional web of material is compressible, which allows the non-woven abrasive material to be pliable and to conform to the surface of work piece. The spring-effect of non-woven abrasive material, allows the brush to conform to irregular surfaces, making complete contact with the work piece.
Not all Non-woven nylon synthetic fibers are created equal.
There are many different chemical formulas developed, that create favorable characteristics, depending on the use of the non-woven abrasive brush final product and desired application use. The thickness and length extruded also develop different three-dimensional patterns that have various effects on the surface conditioning on the work piece surface. Each fiber type produces distinct cutting characteristics because the fiber size is a significant component of the next step, the coating process.
Various patented impregnations and resins continue to be developed, to create favorable characteristics in the final product, a non-woven abrasive brush.
The essential mailability ( softness ) , rigidity ( hardness ), strength, toughness, flexibility, all require a variety of resins to be utilized, to yield the required finish product.
These synthetic impregnations and resins are sprayed and embedded into entire network of nylon fibers, coating them completely. These impregnations create a binder, similar to glue for the abrasive to then be applied.
The two most commonly used abrasives are aluminum oxide ( AlO ) and silicon carbide ( SiC ). The manufacturing of these abrasives are also a patented process that differentiate the quality of a non-woven abrasive brush.
Once the desired abrasive is applied and embedded into to the network of coated fibers, they then go through a UV oven that seals the abrasive to the nylon fibers.
The non-woven abrasive web is then cut into different shapes to create the desired brush.
- Non-woven Abrasive Disc brush
- Non-woven Abrasive Flap brush
- Non-woven Abrasive Convolute brush
- Non-woven Abrasive Hand pads
- Non-woven Abrasive Discs
- Non-woven Abrasive Belts
The manufacturing process of these steps alone, affect the quality of the finished product, Non-woven abrasives brushes for surface conditioning, deburring, cleaning, and finishing the desired work piece.
- Nylon Synthetic Fiber
- Impregnations and binder resins
- Quality, design, and size consistency of the abrasive grit
_____________________________
APT ’s ( Atlantech Process Technology ) manufacturing, design, selection, attention to detail, and procedure, all with state-of-the-art-technology in Germany, set our non-woven abrasive brushes and materials quality, above the rest.
We offer the largest assortment of non-woven material.
- This means we have material available from grit 36 – 1500.
- We selected the very best non-woven material from world wide manufactures to develop the
- We have commercial grade grit in a range, grit sieved several times to yield like size grit, and brushes that have higher grit content for more cutting and finer finishes
Our company technical know-how and manufacturing experience, develop the customized tool for your manufacturing process.
- Increased cleaning, finishing, and/or deburring
- At a lower cost
- Increase line speeds
- Customize brushes to your manufacturing process
- Provide our a precision quality non-woven abrasive and products
- We offer faster delivery than our competition