Wide Face Bristle Brushes
- Cleaning
- Degreasing
- Deoxidizing
- Descaling
- Polishing
- Finishing
Bristle brushes are an all-around tool for general surface cleaning and finishing, for both ferrous and non-ferrous metals.
Metal producers are faced with increasing demands for higher thru-put with a brighter, uniform finish.
APT offers to potential customers, extensive application knowledge and expertise, to provide brushes designed to your process requirements.
IF YOU’RE LOOKING FOR THE BEST BRUSH TO OPTIMIZE YOUR SPECIFIC APPLICATION, YOU SHOULD CALL US!
Characteristics
- Degreasing – applying alkaline, cold detergent, de-mineralized water
- Descaling – removal of mill abrasion and impurity of the strip surface
- Activating – activate and enlarge the strip surface before processing or coating
- Polishing
- Remove pickling residue
- Plating
- Removal of abrasives
- Cleaning of work and backup rolls
- Cleaning of ingot moulds
- Transport rollers for; HHT and NHT furnaces, Electrical Steel, Stainless Steel
Processing Lines
- Strip pretreatment & finishing
- Cleaning lines
- Pickling and annealing lines
- Hot Rolling & Cold Rolling
- Hot dip galvanizing
- Color coating
- Cladding process
- Cleaning of work and support rolls
Technical brushes designed for the perfect fit
APT offers exactly the right brush for our customer’s specific application.
Backed by many years of industrial application & knowledge.
APT makes selecting & implementing better solutions:
FASTER // SIMPLER // MORE RELIABLE & PRODUCTIVE
Details
Packet System
Packet System
APT Packet System for Bristle Brushes
THE APT PACKET SYSTEM is designed to save you time and money by making it easier and faster than ever to refurbish and replace your wide-face brushes.
The brush is assembled in segments (packets) that interlock, making it possible to create a wide-face brush in just the size, radius, and length you need.
All brush segments are delivered dynamically balanced and numbered for immediate installation and use.
Replace & refurbish brushes faster than ever before
- . Save on replacement cost
- . Streamline shipping and delivery logistics
- . Receive refurbished brushes faster
- . Re-build brushes in-house or at your local machine shop
You may not believe it but our welded package system was invented 20 years ago as a development of common spiral brushes with twin tape mounting.
- . Each fill length of a roller brush needed can be divided in a corresponding number of single, compact segments, called packages, that are coiled helixes.
- . What we produce are light and easy-to-handle packages with a constant, high density which facilitates and accelerates the refilling of a brush core or shaft carried out by yourself
- . The twin tape mounting is designed as a concave backing system – as shown below – where the coil widths (WB) range between 5.4 mm to 10 mm. The single coils are spot-welded together without damage to the fill material
- . The bilateral helix ends finish as “carrier noses” that grant a safe driving among the packages and care for a regular surface structure from one segment to the other i.e. no gaps will show up at the segment joints
- . The welded package system is not only easy to mount but it also makes you independent of any transportation of the core to the supplier for refilling, packing, delivery times, etc. and helps you out of emergency situations
- . The stock of replacement cores can be reduced to the minimum.
- . Segments damaged by abrasion due to strip edges, strip joints or strip advance, etc. can be exchanged whereas the non-used brush packages will stay on the brush core or will be mounted together. This means of course an increase of the lifetime limits.
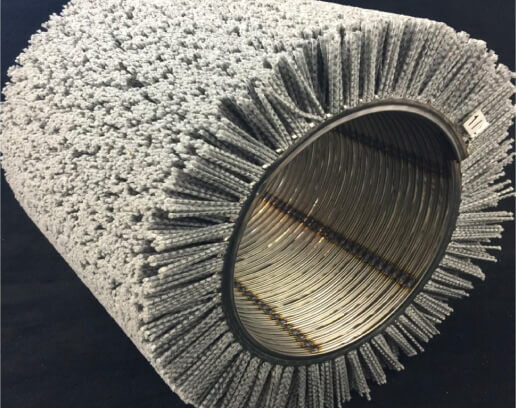
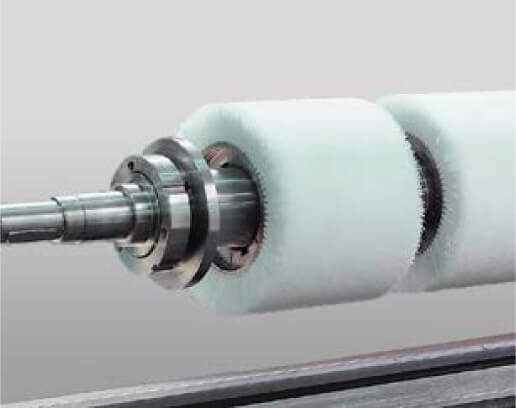
Technical Details
Technical Details
In order to select the best roller brush construction for your purposes we offer the following essential hints:
- . Light- or heavy-duty
- . Operation (i.e. required brushing effect)
- . Immersion depth
- . Fill density
- . Surface or rotational brush speed
- . Forward feed speed of the workpieces
- . Dry or wet operation
- . Low, medium or high temperature
- . Normal or aggressive
- . Medium
- . Required space
- . Correct relation of the brush dimensions (dia.: length/mode of operation) and weight limit.
Light-duty operations
E.g. washing, dusting, polishing, etc.
Heavy-duty operations
E.g. roughening, de-polishing or deadening, deburring of metallic surfaces, removal of residues of sticky, thick or wet material, cement, coal or sand, etc.
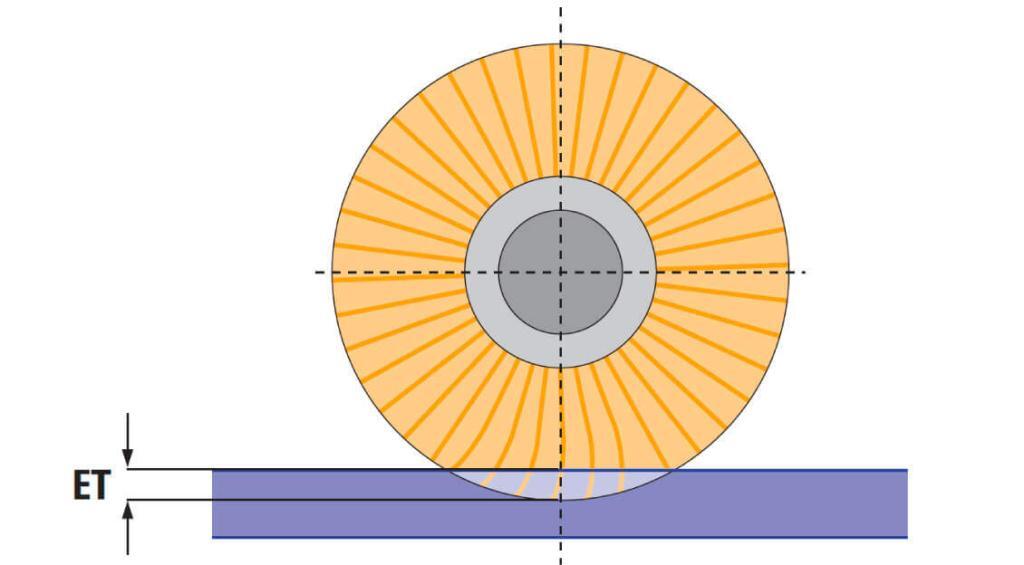
Immersion Depth (ET)
An effective brushing result can be obtained with a slight immersion depth as the brush works correctly with the bristle or wire ends and thus guarantees an even abrasion of the fill material. If the pressure against the workpiece e.g. the immersion depth is excessive the fill material will wear and break very quickly. In order to avoid this situation, we recommend a precisely controlled brush adjustment against the limit stop as essential condition for an optimum immersion depth. The electricity absorption of an idle running serves as the basis. The total electricity absorption is computed using the definition of the immersion depth (pressing on of the brush). We recommend an ongoing control based on the difference electricity absorption.
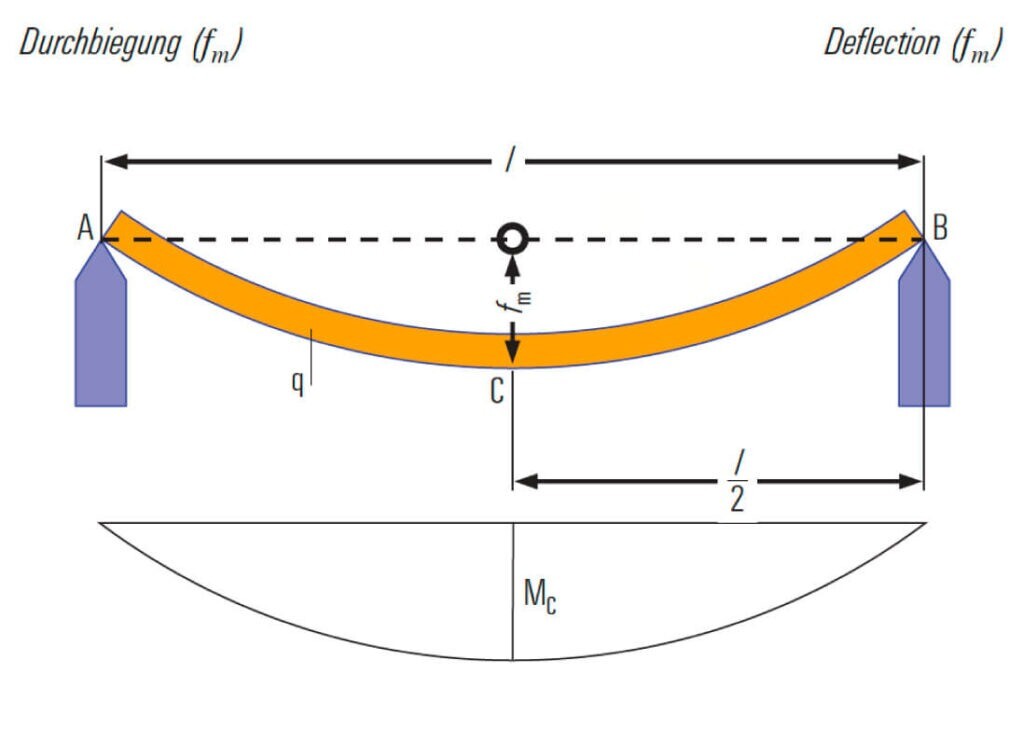
Relationship between brush diameter and length (face width)
The deflection ( “ fm“ ) will be influenced by the following declarations of value: weight of the core and the filling of the brush, distance of bearings, core material and section modulus (depending of cross section of the core). The deflection definite the stability (critical speed) of the rotating roller brush.
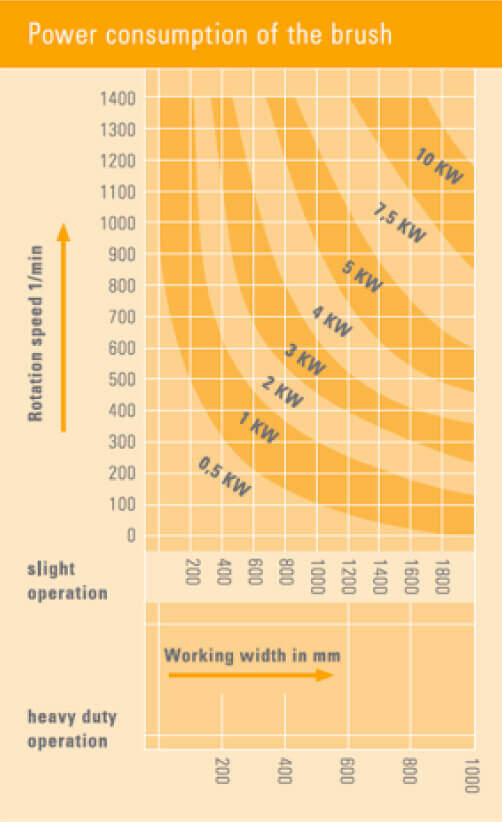
Circumferential and rotational speed / forward feed
These characteristics can only be fixed in relation to the desired brush construction and the working conditions in the customer’s line.
Drive capacity
The drive capacity for roller brushes depends on several conditions and therefore can only be fixed according to all essential data. Please consider the following factors:
Weight: can be influenced by the diameter, length, roller core construction, fixing device and fill material.
Pressure against workpiece: the smaller the immersion depth of the fill material, the lower the drive capacity required.
Fill material: using soft fill materials means a lower resistance whereas a harder, more aggressive fill material requires a higher drive capacity. Our diagram shows typical standard values for the drive capacity for a given diameter of 300 mm.
Surface Speeds (Peripheral Speed in ft/min)
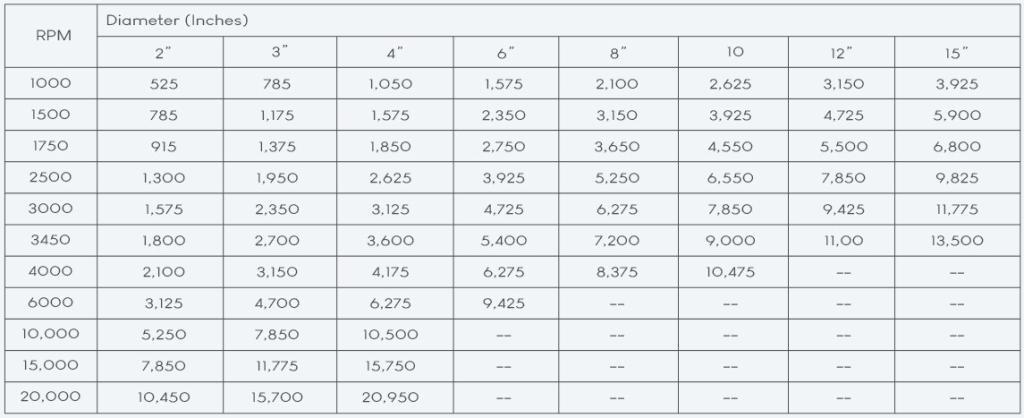
Recommended surface speeds for brushing applications
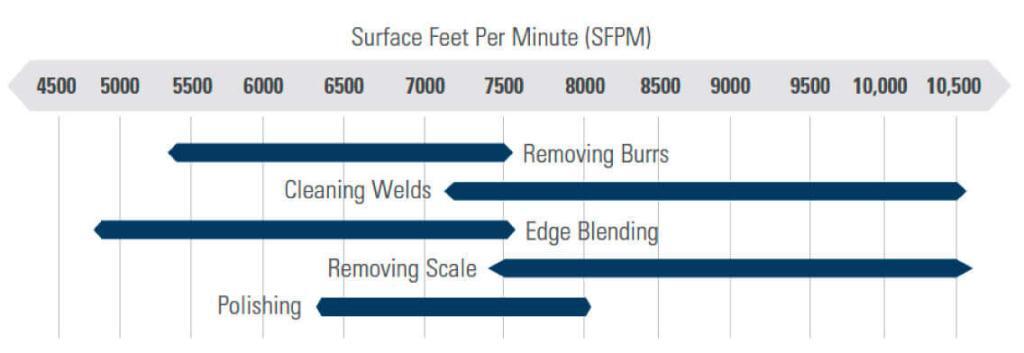
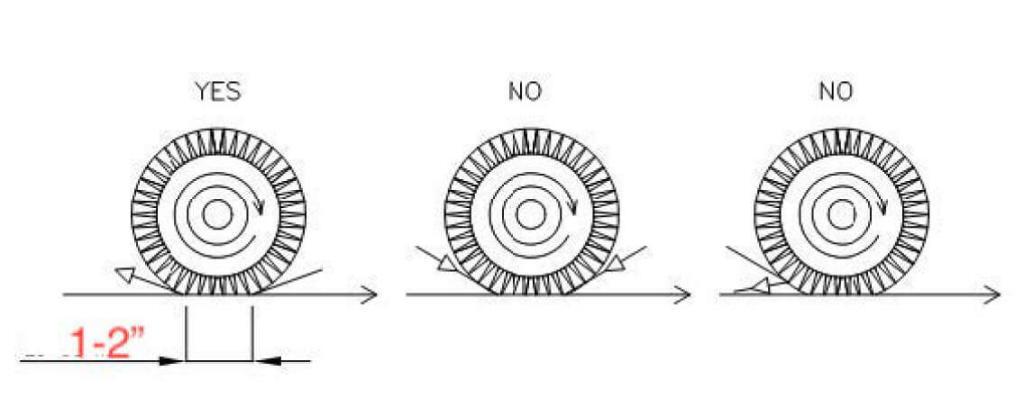
Spraying
The functions and effects of spraying are very important: Incorrect spraying can cause brush damage or catastrophic failure. The spraying system should be checked carefully.
Purpose of spraying:
- . Removal of frictional heat produced at the contact point of brush roll and strip.
- . Removal of particles dispersed from the strip by brushing.
- . Removal of mill oils present on the incoming materials.
Way of spraying:
In order to satisfy the above purposes it is important that ” spraying liquid shall be continuously and uniformly directed into the contact point of strip and brush roll “. The following points are absolutely necessary conditions. Improper spraying contributes to many brush failures.
- . Be sure to spray from the direction the brush is rotating. When the solution is sprayed from the entry into the nip of the brush, it is slung from the nip carrying away the solution, brushing debris, and cooling the bristles. This is not achieved when the spray is directed to the wrong side of the brush engagement.
- . Never spray from both sides of brush roll: as this reduces the efficiency of the cooling and cleaning caused by the solution flow.
- . Never spray to the centre of contact point. when brush roll contacts with strip, its bristles are deflected by about 20mm to 50mm. There fore, the sprayed liquid should applied 10-25 degrees before the con tact point of the strip..
- . As shown , one of the most important factors is the point to be sprayed and the spraying angle shall be adjusted accordingly
- . The spray angle should be set to the proper position for the brush in its engaged position. Do not adjust the spray angle to the brushes raised position as it will be in the wrong position when the brush is engaged.
Brush position control.
Brush position control should be determined by amp draw from the drive motor. Determine the correct amp draw using the following procedure.:
1. Turn on the brush roll without strip material contact, record the power consumption rate and turn off the brush roll
2. Move the brush to just make contact with the strip without deflecting the bristles (only contact without bristles bending).
3. Check to be certain that the brush is perfectly level with the strip to be certain the brush contact is even from one end to the other.
4. Increase the brush engagement and additional 5 mm in depth.
5. Check again to be certain that the brush has traveled perfectly level to the strip and the engagement is the same from side to side on the strip. This will check for backlash in the adjustment system.
6. Start the brush drive and record the amp draw with the strip engaged.
7. The engaged amp draw minus the free amp draw divided by the strip width will be the amp draw per inch or mm of strip. This can be a baseline setting for any strip width. There may be a need to adjust this amount under certain conditions such as a brush which is near minimum diameter may require a slight decrease in amp draw per inch or mm based on the smaller diameter and moment of inertia. Smaller diameters require less torque.
Trimming and total and partial repair/recovering:
If brush roll is working at specified amp draw and the bristles don’t touch the strip surface in the center, the brush will require dressing. The brush can be dressed with some standard equipment or sent to your authorized distributor.
When the bristles of brush roll are totally worn, (5-10 mm. length from the metallic plates) it is necessary to replace all of the brush segments.
Remove the brush from the line.
Important Notice: We recommend a complete shaft inspection and check for runout between centers before installing new brush segments each time. In case of excessive runout or dimensional issues, repair and certify that the shaft is dynamic balanced at G-2.5.
Working, Handling and Storage recommendations:
Working:
- . Never stop the brush in contact with the strip or back roll : bristles will be permanently deformed and damaged
- . Never stop the line in contact with the brush roll (even in wet conditions) and never stop the brush roll spraying system: synthetic bristles can melt if heat from friction causes them to over heat.
Handling:
- . Never pick up the brush roll by the bristles
- . Always pick up the brush roll by the shafts necks
- . Cover and protect the shaft necks before picking up the roll
Storage and/or Shipment:
- . Nothing should touch the brush roll bristles
- . Cover the brush with a plastic or paper
- . Always pick up the brush roll by the shafts necks
- . Protect the metallic shaft necks with a anticorrosion oil and cover with an anti-static protection
- . If shipment is required, wrap the brush roll and use a closed wood box or similar protection (remember that inside of the box nothing should touch the brush roll bristles)
Important Notice: All statements, technical information and recommendations contained herein are based on tests we believe to be reliable, but the accuracy or completeness thereof is not guaranteed, and the following is made in lieu of all warranties expressed or implied: Sellers and manufactures only obligation shall be to replace such quantity of the product proved to be defective. Neither seller nor manufacturer shall be liable for any injury, loss or damage, direct or consequential, arising out of the use of or inability to use this product.
Applications
Applications
Metal surfaces must be cleaned before being processed in the finishing lines in the primary metal industry. This cleaning process is very important to guarantee a consistent annealing and galvanized coating process of metallic coils.
The common practice is use a chemical and brushing process. The coil surface is treated with alkaline and/or electrolytic alkaline cleaning systems and mechanical brushing in order to remove the maximum possible amount of metallic fines and oils from coil surfaces.
During the process, a hot chemical solution and electrolytic ionization separate the oils and metallic particles from the coil surface and the brushes remove it mechanically.
This combination of chemical and mechanical process is the best system to clean the coils surfaces, but today the customers are pushing to improve cleaning and increase line speed in existing or in new cleaning equipment.
The problem is that the conventional cleaning sections or lines have a big limitations to their cleaning performance.
Current lines configurations do not have free space to add new degreasing, electrolytic or brushing units and the costs for these line modifications are very expensive and the production cost per ton will increase proportionally with the addition of this new equipment.
Industry Applications
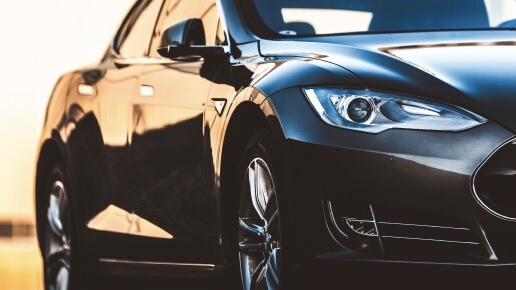
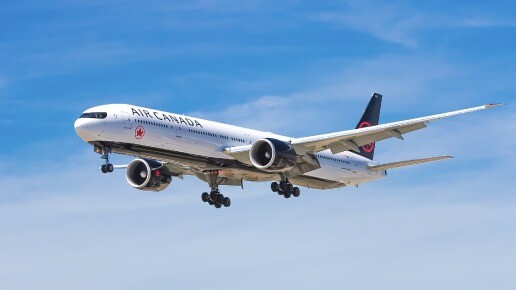
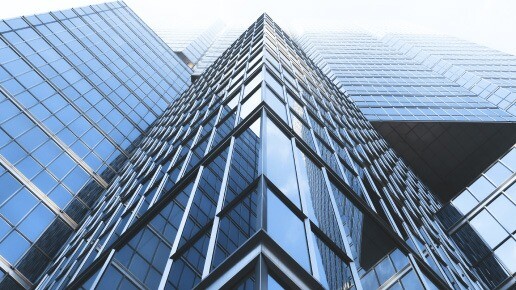
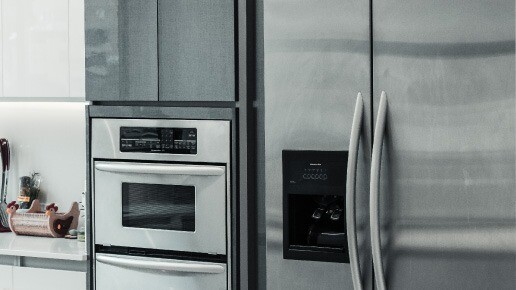
. keying
. removing of dirt
. removing of blasting abrasives
. smoothing
. creating of bare surfaces
. finishing of surfaces
. cleaning
. transporting
. covering
. antistatic
. creating of bare surfaces
. noise reduction
. cleaning
. oiling
. cleaning of forms
. cleaning of pressing boards
. cleaning of paling-boards
. superimposing of a liquid
. dust collecting, dedusting
. conveyor-belt cleaning
. smoothing
. matting
. cleaning of pressing boards
. cleaning
. grinding
. structuring
. spreading
. keying
. deburring of edges
. counter-pressure
. cleaning of paling-boards
. dust collecting
. de-dusting
. removing of blasting abrasives
. deburring of surfaces
. deburring of edges
. derusting
. matting
. finishing of surfaces
. deburring of surfaces
. deburring of edges
. removing of dirt
. deburring of edges
. Industry generally
. removing of blasting abrasives
. deburring of surface
. braking
. noise reduction
. matting
. polishing
. structuring
. aesthetic refinement
. cleaning of baking trays
. conveyor-belt cleaning
. drum cleaning
. drum cleaning
Process Line Material Types:
- . Steel
- . Stainless steel
- . Aluminium
- . Heavy metal strips
- . Strip pretreatment & finishing
Electrolytic processing of:
- . Zinc
- . Tin
- . Chromium
- . Nickel
- . Brass
- . Copper
Brush Machine Applications for Strip Production
- . The descaling process
- . In order to remove pickling residue
- . In degreasing lines applying alkaline, cold detergent, de-mineralised water or the electrolytic degreasing process
- . To avoid the silver-bronze-effect on stainless steel sheets i.e. reduction of the depth of roughness
- . For removal of mill abrasion and impurity of the strip surface
- . To activate and enlarge the strip surface before processing or coating
Process Line Operations:
- . Pickling lines
- . Cleaning lines
- . Pickling and annealing lines
- . Continuous annealing lines
- . Bright annealing
- . Hot galvanizing with
- .Zinc, Aluminium-zinc and other alloys
- . Color coating
- . Cladding process:
- . to obtain ply metal (e.g. copper/aluminum) as one of the most important conditions to get a perfect adherence of the plated metals is an absolutely degreased and metallically pure strip surface and a subsequent activating and roughing to enlarge the surface.
-
- . Cold Rolling cladding of composite materials:. An important requirement for a good adhesion of the “clad ding partners” is a totally grease and free of metal fines on the strip surface with a following activation and roughening to in crease the surface..
- Hot Rolling
- . descale metal sheets before and after the straightening ma chine in steel hot rolling mills with an aggressive wire fill mate rial even in warm conditions up to 1,000 °C.
Brush Solutions For:
- . SKIN PASS MILL
- . COLD ROLLING STANDS
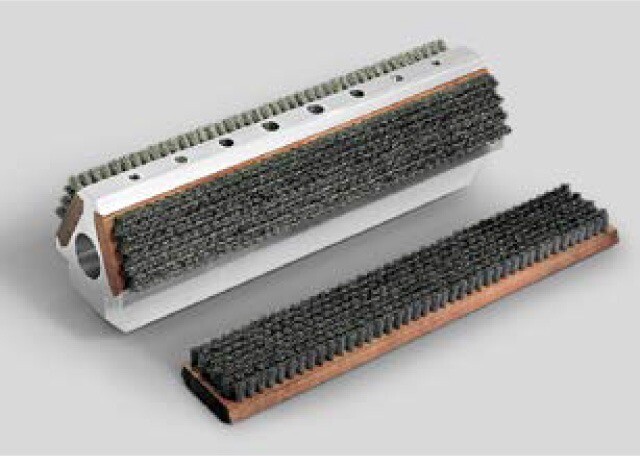
Effective Cleaning:
Cleaning with lath brushes, a long lifetime will be achieved. In addition, pollution will be reduced by dry-cleaning with extraction function. The brush filament contains many elastic wire tips. The wire can make the rollers clean without changing the surface roughness, such as filaments with abrasive grain.
Special brushes for cleaning of work and support rolls at the same time:
This brush consists of an aluminum core with dovetail grooves and inserted cleaning strips, as well with lateral sealing strips if required. Dirt will be removed by special slots between the cleaning and sealing strips. Therefore, the aluminum core equips two bores at the bottom for connection with the extraction system.
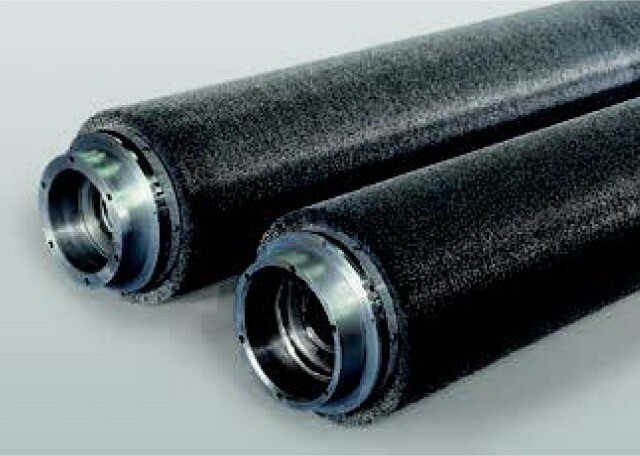
Roll Cleaning Device:
Working and supporting rolls are cleaned by oscillating roller brushes.
How to arrange your roller brushes
- Supporting rolls
- Working Rolls
- Roller brushes for cleaning
- a. Supporting rolls
- b. Working rolls
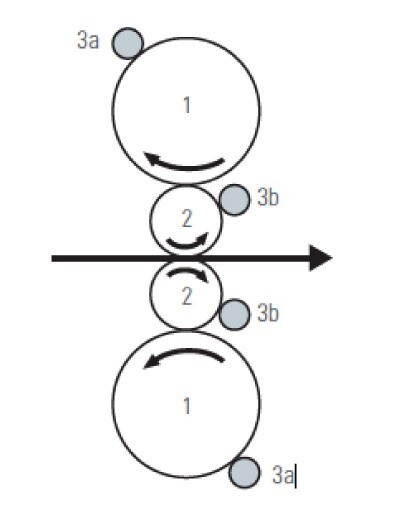
Strip processing line
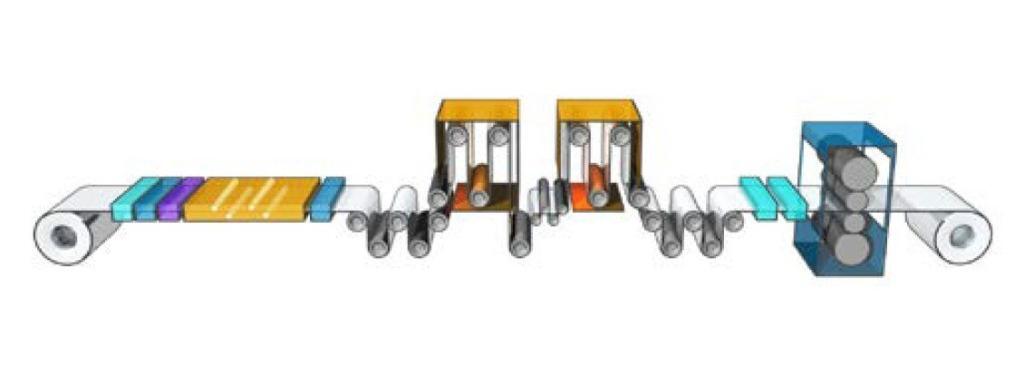
1. Strip processing (furnace)
2. Cooling tower
3. Skin pass mill
4. Cleaning roller brushes
5. Exit looper
6. Entry looper
7. Strip processing brushes
Rolling Mills:
These high density brushes were constructed for special brushing machines in order to work at extreme conditions and to obtain an intensive brushing effect – hence the name.
The intensive results are due to specially ground brush surface and the highly precise production process.
We also manufacture cores with an inside floating system on request and offer a perfect brush concentricity due to our balancing to standard G 2.5, according to ISO 1940.
We also might point out that in many fields of strip production the intensive brushing effect is a necessity to obtain a surface quality standard required by the manufacturing industry.
Application Purposes:
APT’s abrasive roller brushes also offer a considerable cost-performance ratio in particular when applied in:
- . Pickling-annealing lines for hot rolled stainless steel strips to support descaling and reduction of the depth of roughness.
- . Electrolytic processing lines at the end of the lines as “polishers.”
Aluminum Rolling Mills:
Applying our brushes on hot-rolled strip surfaces free of striation are an important quality requirement of the manufacturing industry, regarding the grade of cold-rolled strips. In the cleaning process of working rolls in aluminum hot rolling mills, normally oscillating roller brushes are used for removal of the alum num-oxide layer, which was built during the rolling process. A slight and even particle coating must remain on the strip.
We optimized the construction of our roller brushes and adapted them exactly to the working conditions in rolling stands i.e.
- . The corresponding cleaning devices
- . The rolling emulsion used
- . The surface quality of the working rolls.
Our brushes have kept up perfectly with these complex tasks in various rolling mills in Germany and USA for decades due to continuous development.
Brush qualities:
- . High fill density
- . A surface perfectly trimmed and ground for concentricity or, if required, a ground surface trim either convex or concave.
- . Electro-dynamically balancing, as per the required rotation speed limit, balancing grade G 2,5 according to ISO 1940.
Fill qualities:
According to the working conditions in the mill we offer different:
- . Steel wire qualities
- . Stainless steel wires
- . Abrasive bristles with various grit sizes
Cold Rolling Stands:
In cold rolling mills the operators normally use roller brushes with a soft synthetic fill material for cleaning processes:
- . removal of very fine aluminum particles from deflection and measuring rolls, working or support rolls.
Furthermore our brushes are applied for surface treatment of strips and sheets, for instance:
- . For de-polishing or dulling (e.g. decorative surfaces or litho-quality)
- . For roughening before coating
FAQ
Frequently Asked Questions
Our brushes are used in many branches. The product range thus consists of a wide selection of industrial and technical brushes.
Our standard or customized products ensure that you get the brush that meets your objectives. Our objective is to ensure that our brushes provide additional value to our customer’s production processes.
Brushes fulfill often inconspicuous but essential functions within the production process. Almost everywhere where products or materials have to be manufactured or treated, you will discover brushes.
Advantages of APT bristle brushes:
- . They are versatile and offer a flexible solution for often complex industrial processes
- . They improve, accelerate and optimize various production processes
- . They prevent production interruptions and reduce downtime
- . They treat products and materials with care
- . There are many types of brushes and materials possible, so we can always offer the right solution
Common issues:
Brushing effect too weak
- . Increase the peripheral speed by increasing the brush diameter or the operating speed (observe the max. safety speed)
- . Decrease the trim length
- . Increase the diameter of the filling material
Brushing effect too powerful
- . Reduce the peripheral speed by reducing the brush diameter or the operating speed
- . Increase the trim height
- . Decrease the diameter of the filling material
Surface finish too rough
- . Increase the peripheral speed by increasing the brush diameter or the operating speed (observe the max. safety speed)
- . Increase the trim height
- . Decrease the diameter of the filling material
Surface finish too smooth
- . Reduce the peripheral speed by reducing the brush diameter or the operating speed
- . Decrease the trim length
- . Increase the diameter of the filling material
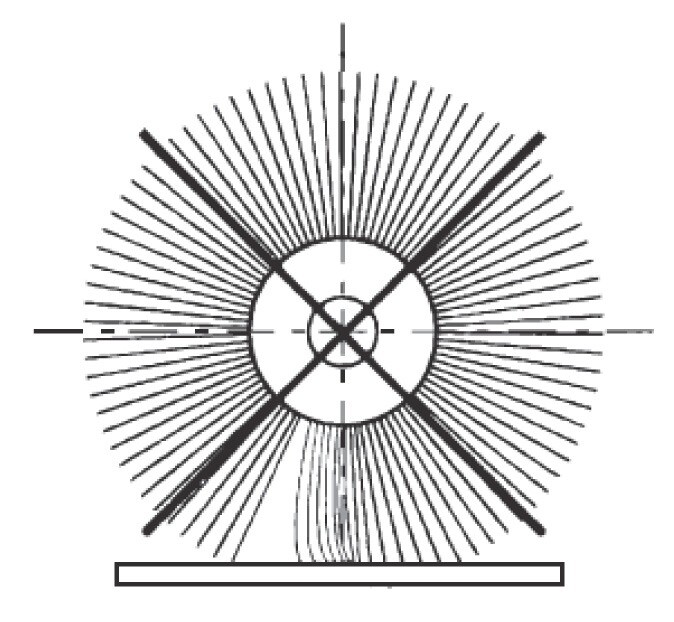
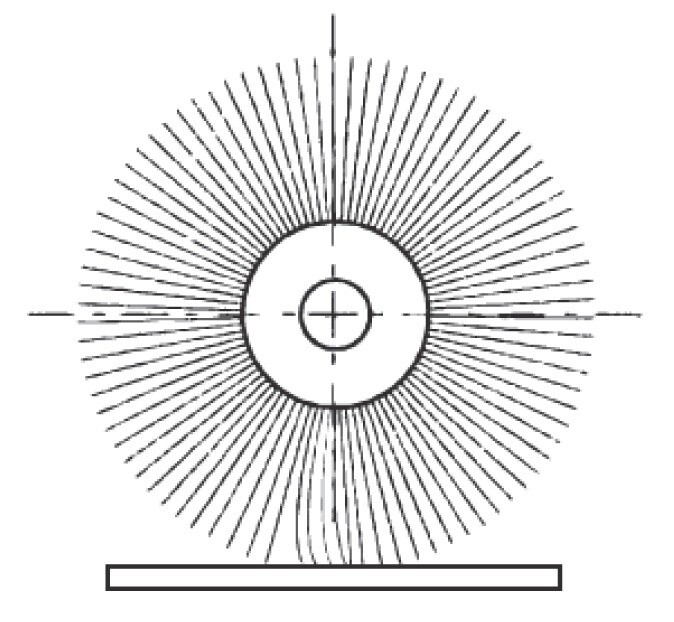
10 Factors for good brushing
The bristles of a brushing roll have two main functions:
- . They pass on the impact strength to the bristle tip
- . The contact / friction on the metal surface
By optimizing these functions the working capacity of the brush improves.
________________________
1. Filaments:
Filaments are selected according to the required brush applications:
- . To clean sensitive oily surfaces, ultra fine filaments are used
- . For thick sheet stripping / descaling, it is necessary to increase the brush strength/stiffness, very thick filaments are used
- . Different materials are used according to the various chemical solutions and temperatures in which the brush will be used
2. Abrasive Charges:
Filaments can contain several abrasive powders of different grain in order to increase the cleaning and grinding capacity of the coil material.
3. Size and Geometry of the bristles:
Bristles can be formed in fine or coarse sizes in order to increase or reduce the impact on the sheet and grip of the material.
4. Length of Bristles:
The ideal length should be between 1-2” according to the application and the maximum acceptable diameter of the brush equipment.
5. Brush External Diameter:
- . The brush external diameter affects the cleaning capacity
- . The impact strength of the bristles depends on the circumferential speed of the roll surface
- . The grip capacity depends on the frictional pressure at each turn of the roll
- . This increases as the diameter increases and contains more bristles per sq. in.
It is important to bear in mind that the external diameter of the brush is mostly limited by the length of the bristles and the brushing equipment.
6. Brush Rotation Speed:
A minimum of 750 rpm and a maximum of 1000 rpm is recommended.
7. Density of the Bristles on the surface:
- . High density improves the cleaning capacity and the brush service life
- . Does not allow water flow between bristles and often get damaged by lack of cooling and by excess of dirt
- . Brushes get damaged because of these reasons
8. Binding – distribution of Bristles:
Bristles should be distributed evenly on the brush surface. The configuration must allow the flow of water between the bristles for them to cool adequately and to facilitate the outlet of dirt and the cleanliness of bristles using the centrifugal force. Grouped bristle configuration in tufts is very effective because it improves bristle impact strength and it allows water to flow between bristles avoiding damage.
9. Brush adjustment on sheet metal:
This must be selected for each type of brush. On average, brushes have to be adjusted between 1-3 mm depth in relation to the sheet surface. It is advisable that these positions should be controlled automatically by the brush equipment.
10. To sprinkle water on the brushes:
Sprinkling water on the synthetic brush bristles is necessary. The main objective is to avoid heating generated by the friction of bristles against the metal – especially if bristles contain abrasive powder -, but it also allows the transfer of dirt or metal residues from the plate surface and keeps brush bristles clean. Furthermore, the cleaning effect can be increased by degreasing alkaline solutions sprinkled with water.
Safety Recommendations
Safety Recommendations
Safety recommendations for the correct handling of power-driven brushing tools
EN 1083-2 regulates safety requirements imposed on power-driven brushing tools. The safety speed stipulated on the brush, the label or the packaging must not be exceeded. In some cases, the recommended working speed may be well below the maximum safety speed. The rotating speed of the drive machine may never exceed the maximum safety speed for the brushing tool. In order to increase safety when working with power-driven brushing tools, please additionally observe the following measures.
Before operation
- . All operators must read, study, understand and comply with all warnings and operating instructions and those instructions provided with the power tool before using this brushing tool
- . Use only brushing tools that are applicable for the machine
Storage of brushes
- . Brushing tools must be stored in the relevant containers and in suitable rooms and be protected from deformation
- Brushing tools must be protected from high humidity, condensation, heat, liquids or steam which might cause damage to the brush or oxidation of components
User protection
- . Check power driven brushes before each use on possible damages and scrap the brush if necessary
- . Power driven brushes may loose filaments and eject particles and debris, which can damage the body and easily penetrate thin clothing and/or the skin. All persons in the working area must wear suitable personal protective equipment: safety glasses/full face shield, safety gloves, ear protection, protective clothing, respiratory protection against dust and fumes
Mounting and operation
- . Make sure that the power driven brush is suitable for the intended application
- . The marked maximum permissible speed of rotation Max RPM or max or MSFS must never be exceeded
Brushing tools shall be used only on machines with suitable clamping
- . Connection Threads of machine and brush shall be equal
- . When working with shaft-mounted brushes, the marked minimum clamping length or maximum free shaft length shall be followed
- . Do not clamp on the radius of the shaft, but the cylindrical area only
- . Brushing tools with metallic adapters or plastic bushings must be clamped on the original metal flanges, and not on the adapters
- . Do not overload the brush by too high contact pressure
- . Please check brushing tool and machine when it comes to high vibration
- . Tube brushes shall be used only inside a tube or a hole when they are power driven
- . Tool guards must be kept in place at all times
Disposal
- . Worn or damaged brushes must be properly disposed of in accordance with local authority regulations
Due to the large variety of machine types and applications, the safety instructions listed here cover fundamental safety aspects. For more information and recommendations, please refer to the relevant laws, regulations, safety instructions and standards.
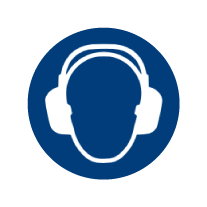
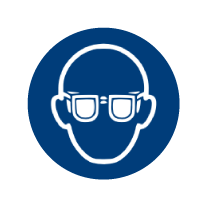
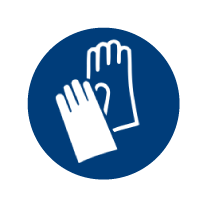
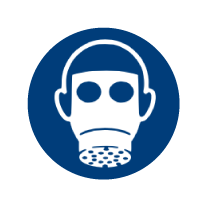
WARNING!
FAILURE TO OBSERVE SAFETY PRECAUTIONS MAY RESULT IN INJURY.
Warning: In normal power brushing operations, the material being removed, such as burrs, scale, dirt, weld slag or other residue, will fly off the brush with considerable force along with brush filaments which break off due to fatigue.
The POTENTIAL OF SERIOUS INJURY EXISTS for both the brush operator and others in the work area (possible 50 or more feet from the brush).
To protect against this hazard,
WEAR SAFETY GOGGLES or FULL FACE SHIELDS WORN OVER SAFETY GLASSES WITH SIDE SHIELDS, along with PROTECTIVE CLOTHING.
You must follow all operator and safety instructions, as well as all common safety practices which reduce the likelihood of physical injury, or reduce its severity.
Safety Goggles- Safety goggles or full face shields worn over safety glasses with side shields MUST BE WORN BY ALL OPERATORS and OTHERS IN THE AREA of power brush operations.
Comply with the requirements of ANSI Z87.1-1989 “Occupational Eye and Face Protection.” Guards- Keep all machine guards in place.
Safety Standard Speeds- Observe all speed restrictions indicated on brushes, containers, labels, or printed in pertinent literature. “MSFS” means Maximum Safe Free Speed (RPM) – spinning free with no work applied. For reasons of safety “MSFS” should not be exceeded under
any circumstances.
Safety Standard- Comply with the Safety Standards of the Industrial Division of the American Brush Manufactures’ Association and the American National Standards Institute ANSI B165.1-2000 – Safety Requirements – Power Brushes and ANSI B165.2-1982” Safety Requirements- Power Brushes – Wood, Plastic, or Composition Hubs.
Important Notice: All statements, technical information and recommendations contained herein are based on tests we believe to be reliable, but the accuracy or completeness thereof is not guaranteed, and the following is made in lieu of all warranties expressed or implied: Sellers and manufactures only obligation shall be to replace such quantity of the product proved to be defective. Neither seller nor manufacturer shall be liable for any injury, loss or damage, direct or consequential, arising out of the use of or inability to use this product.